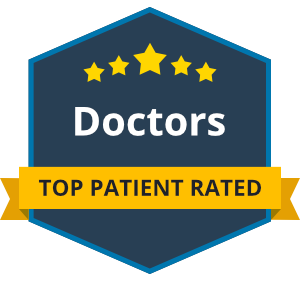
Find Local Doctors Directory – Easily Find Top Patient Rated Doctors
Are you looking for a doctor or dentist to provide treatment for you or for a member of your family? Whether you are looking for a family dentist, an oral surgeon, an OBGYN or a plastic surgeon, we can help.
Our extended physician and medical practice profile pages are a great introduction to the doctors in your area. Find Local Doctors also provides direct links that help you quickly locate reviews about the physician or medical practice that you are considering.